OEE (Overall Equipment Effectiveness) to istotne narzędzie do mierzenia efektywności procesów produkcyjnych. Ważne jest, aby umieć je właściwie obliczać i rozumieć jego wyniki. W artykule znajdziesz wyjaśnienia dotyczące znaczenia OEE, jakie informacje są kluczowe do jego analizy oraz typowe błędy pojawiające się podczas jego obliczania. Dodatkowo, przedstawione są metody zwiększania wartości tego wskaźnika, co może prowadzić do poprawy wydajności i jakości produkcji.
Co to jest wskaźnik OEE?
Wskaźnik OEE, czyli Ogólna Efektywność Wyposażenia, jest ważnym miernikiem w branży produkcyjnej, oceniającym sprawność maszyn. Składa się z trzech kluczowych elementów:
- dostępności,
- wydajności,
- jakości.
Pozwala to na wyrażenie efektywności urządzeń w procentach. Jest to iloczyn tych trzech wskaźników, umożliwiający dokładną ocenę procesów produkcyjnych. Dzięki analizie OEE przedsiębiorstwa mogą lepiej zrozumieć wydajność swoich maszyn i zlokalizować obszary wymagające usprawnień. To z kolei przyczynia się do podwyższenia ogólnej efektywności sprzętu.
Dodatkowo, ten wskaźnik stanowi cenne narzędzie w strategiach ciągłego doskonalenia produkcji, pomagając eliminować marnotrawstwo i tym samym podnosić konkurencyjność na rynku.
Dlaczego wskaźnik OEE jest ważny w produkcji?
Wskaźnik OEE (Overall Equipment Effectiveness) ma ogromne znaczenie w przemyśle produkcyjnym. Umożliwia przedsiębiorstwom precyzyjną ocenę wydajności zarówno maszyn, jak i całego procesu. Dzięki niemu można zidentyfikować wąskie gardła ograniczające efektywność, co pozwala na podejmowanie trafnych decyzji optymalizujących produkcję, skutkując wzrostem efektywności oraz obniżeniem kosztów.
OEE odgrywa również kluczową rolę w kontekście Przemysłu 4.0, gdzie monitorowanie efektywności urządzeń w czasie rzeczywistym staje się standardem. Wspiera strategie ciągłego doskonalenia poprzez eliminację marnotrawstwa i poprawę jakości towarów. Przejrzystość danych motywuje załogę do większej wydajności, co jest niezwykle ważne w systemach premiowych opartych na KPI.
Dodatkowo, OEE pozwala na porównywanie wydajności różnych linii produkcyjnych w firmie, co ułatwia podjęcie decyzji o inwestycjach w nowoczesne technologie lub restrukturyzacji procesów. Dla przedsiębiorstw dążących do zwiększenia konkurencyjności, stanowi ono niezastąpione narzędzie do analizy efektywności.
Jak obliczyć wskaźnik OEE?
Aby obliczyć wskaźnik efektywności ogólnej urządzeń (OEE), korzystamy z prostego równania: OEE = Dostępność × Wydajność × Jakość. Każdy z tych składników odzwierciedla różne aspekty wydajności produkcji.
Dostępność określamy jako proporcję między faktycznym czasem pracy a planowanym czasem działania. Posługujemy się tu wzorem A = APT/PBT, gdzie APT oznacza rzeczywisty czas pracy, a PBT to czas planowany.
Wydajność mierzymy, porównując planowany czas na jednostkę z faktycznym czasem potrzebnym do wykonania pojedynczego produktu. Wzór ten wygląda następująco: E = PRI*PQ/APT. PRI to czas przewidywany na jednostkę, PQ odnosi się do liczby wyprodukowanych produktów, a APT jest rzeczywistym czasem pracy.
Jakość to stosunek liczby produktów spełniających normy do całkowitej ilości wyprodukowanych jednostek. Wyrażamy to wzorem QR = GQ/PQ, gdzie GQ to liczba produktów o odpowiedniej jakości, a PQ to całkowita ilość wyprodukowanych produktów.
Dokładność wskaźnika OEE zależy od precyzji danych dotyczących produkcji, takich jak planowane i rzeczywiste godziny pracy maszyn, ilość produktów oraz przewidywane czasy operacji. Ustalenie tych parametrów jest kluczowe dla uzyskania wiarygodnych wyników.
Jakie dane są potrzebne do analizy OEE?
Analiza wskaźnika OEE wymaga starannego gromadzenia informacji w trzech istotnych obszarach: dostępności, wydajności i jakości.
- dostępność – aby ocenić dostępność, należy porównać zaplanowany czas pracy maszyny z rzeczywistym okresem jej działania, dane te mogą pochodzić z harmonogramu produkcji lub kalendarza pracy urządzenia i mogą być rejestrowane zarówno automatycznie, jak i ręcznie,
- wydajność – analizujemy, zestawiając normatywne czasy operacji z faktycznym czasem potrzebnym do wytworzenia określonej ilości produktów, do tego niezbędne są informacje o przewidywanym czasie na jednostkę oraz liczbie wyprodukowanych wyrobów,
- jakość – mierzymy, porównując liczbę produktów spełniających normy z całkowitą ilością wyprodukowanych jednostek, dzięki temu można dokładnie określić, ile z wyrobów spełnia wymagane standardy.
Dokładne informacje produkcyjne są kluczowe dla precyzyjnej analizy OEE. Pozwalają one na optymalizację procesów oraz podejmowanie lepszych decyzji w zarządzaniu produkcją. Co więcej, wdrożenie systemów do monitorowania czasu pracy oraz automatyzacja danych produkcyjnych mogą znacznie zwiększyć dokładność i efektywność analizy wskaźnika OEE.
Najczęstsze błędy przy obliczaniu OEE
Błędy podczas obliczania OEE często wynikają z nieprawidłowego gromadzenia danych dotyczących produkcji. Niewłaściwe określenie całkowitego czasu pracy lub pominięcie nieplanowanych przestojów, takich jak awarie maszyn czy przezbrojenia, może prowadzić do zniekształcenia wyników. Kluczowe jest uwzględnienie wszystkich elementów mających wpływ na OEE, w tym strat produkcyjnych oraz defektów procesu.
Często zapomina się o marnotrawstwie, które również wpływa na spadek efektywności. Istotne jest dokładne określenie czasu planowanego i rzeczywistego oraz szczegółowa analiza strat efektywności. Dzięki temu możliwa jest rzetelna ocena wskaźnika oraz identyfikacja obszarów wymagających poprawy.
Jak poprawić wartość wskaźnika OEE?
Zwiększenie wskaźnika OEE to zadanie wymagające wszechstronnego podejścia do usprawnienia procesów produkcyjnych. Niezbędne jest ograniczenie strat oraz poprawa efektywności maszyn. Dzięki automatyzacji można zminimalizować błędy i skrócić czas przestojów, co przekłada się na lepszą dostępność urządzeń. Systemy IT do monitorowania jakości pozwalają na szybkie wykrywanie defektów, co z kolei podnosi standardy produkcji.
Udoskonalenie metod wytwórczych można osiągnąć poprzez wdrożenie takich strategii jak:
- Lean Manufacturing,
- TPM (Total Productive Maintenance),
- Six Sigma,
- Teoria Ograniczeń.
Te podejścia koncentrują się na redukcji marnotrawstwa i zwiększeniu zaangażowania zespołu. Lean Manufacturing kładzie nacisk na nieustanne doskonalenie i eliminację niepotrzebnych elementów, natomiast Six Sigma wykorzystuje analizę statystyczną do zmniejszenia zmienności i poprawy jakości. Teoria Ograniczeń umożliwia identyfikację i eliminację wąskich gardeł w produkcji. Implementacja tych strategii prowadzi do lepszego OEE poprzez wzrost wydajności i jakości.
Kluczowe znaczenie ma raportowanie wyników oraz analiza danych produkcyjnych, które pomagają wskazać obszary wymagające poprawy. Dzięki temu przedsiębiorstwa mogą dokonywać przemyślanych inwestycji w nowe technologie lub zmiany procesów. Ulepszenie OEE nie tylko podnosi efektywność, ale również redukuje koszty operacyjne, co jest istotne dla utrzymania konkurencyjności na rynku.
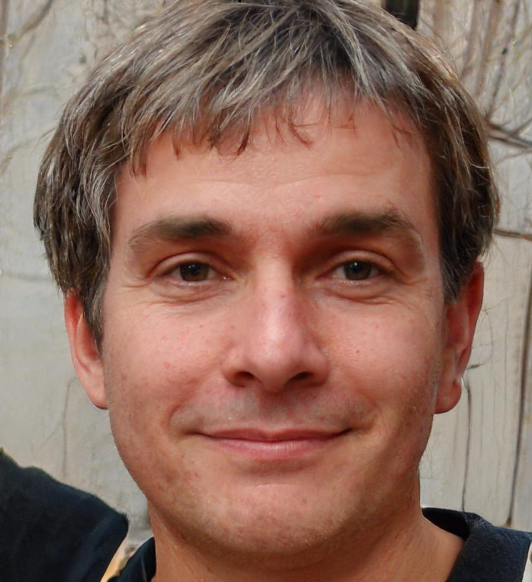
Nazywam się Jakub i jestem logistykiem z 15 letnim doświadczeniem. Pracowałem w różnych firmach i obecnie pracuje wyłącznie z domu obsługując zlecenia różnych firm. Na blogu dzielę się z Wami moją obszerną wiedzą o logistyce i produkcji.