Zaawansowane Planowanie Jakości Produktu (APQP) to skomplikowana metodologia, kluczowa zwłaszcza w sektorze motoryzacyjnym. Postaramy się przybliżyć, czym dokładnie jest APQP, jakie przynosi korzyści oraz jakie pięć kluczowych etapów obejmuje. Dodatkowo omówimy narzędzia wspomagające jego wdrożenie. Zrozumiesz, w jaki sposób APQP może usprawnić procesy produkcyjne i podnieść jakość produktów finalnych.
Co to jest APQP i jakie ma znaczenie?
APQP, czyli Zaawansowane Planowanie Jakości Produktu, to uznany proces zarządzania jakością, który obejmuje wszystkie kluczowe etapy, od koncepcji aż po produkcję seryjną. Dzięki temu podejściu można skutecznie kontrolować jakość na każdym etapie rozwoju produktu, zapewniając jednocześnie klarowną komunikację z dostawcami i uporządkowanie całego procesu produkcyjnego.
Wykorzystanie APQP zmniejsza ryzyko nieporozumień związanych z wymaganiami technicznymi oraz umożliwia szybkie identyfikowanie potencjalnych problemów. Dzięki temu koszty i czas wprowadzania nowych produktów na rynek są znacznie zoptymalizowane. System ten powstał w latach 80. w branży motoryzacyjnej, ale z powodzeniem stosuje się go również w innych sektorach, takich jak lotnictwo czy elektronika użytkowa. APQP jest nieodzownym elementem zarządzania projektami, zwłaszcza gdy chodzi o spełnianie wysokich standardów jakości.
Jakie są kluczowe korzyści z zastosowania APQP?
APQP, czyli Zaawansowane Planowanie Jakości Produktu, przynosi wiele korzyści producentom OEM oraz ich dostawcom. Jednym z kluczowych atutów jest przyspieszenie wprowadzania nowych produktów na rynek, co pozwala firmom na szybką adaptację do zmieniających się oczekiwań konsumentów i wymagań rynkowych. APQP zapewnia strukturalne umowy i procedury dotyczące definiowania oraz wymagań produktów, co ułatwia komunikację z dostawcami i ocenę możliwości produkcyjnych.
Dzięki temu systemowi można zminimalizować problemy wynikające z niepoprawnej interpretacji specyfikacji technicznych, co zmniejsza ryzyko w procesie produkcji. Umożliwia on wczesne identyfikowanie potencjalnych problemów już na etapie projektowania, co zapobiega wytwarzaniu części niespełniających norm jakości. W rezultacie efektywność produkcji wzrasta, a produkty lepiej odpowiadają wymaganiom, co przekłada się na większe zadowolenie klientów.
APQP to także skuteczne narzędzie do redukcji kosztów związanych z późniejszymi modyfikacjami produktów, co jest korzystne dla całego łańcucha dostaw. Dlatego metoda ta jest szeroko stosowana nie tylko w przemyśle motoryzacyjnym, ale także w lotnictwie i elektronice użytkowej.
Pięć faz APQP – jak przebiega proces?
Pięć etapów APQP to fundamentalne kroki, które gwarantują wysoką jakość produktu oraz efektywność jego wytwarzania.
- pierwszy z nich obejmuje planowanie oraz definiowanie programu,
- następnie przechodzimy do projektowania i rozwoju produktu,
- kolejny etap koncentruje się na projektowaniu i rozwoju procesu produkcyjnego,
- w czwartym etapie dochodzi do zatwierdzenia zarówno produktu, jak i procesu,
- piąty, finałowy etap, to pełnoskalowe uruchomienie produkcji oraz ocena i optymalizacja procesu.
Na etapie planowania określamy cele dotyczące jakości, harmonogramy oraz oczekiwania klienta. Projektowanie i rozwój produktu wiążą się z tworzeniem dokumentacji technicznej oraz testowaniem prototypów. Projektowanie i rozwój procesu produkcyjnego obejmują analizę ryzyka i projektowanie samego procesu. Zatwierdzenie produktu i procesu odbywa się poprzez walidację z wykorzystaniem próbki produkcyjnej oraz procesu PPAP. Pełnoskalowe uruchomienie produkcji wiąże się z naciskiem na ciągłe doskonalenie i analizę informacji zwrotnej z rynku.
Każdy z tych etapów, będący częścią uruchomienia, posiada swoje kluczowe zadania i działania zapobiegawcze, które są niezbędne do sukcesu projektu.
Jakie narzędzia wspierają APQP?
W procesie APQP kluczową rolę odgrywają narzędzia wspomagające, które wspierają planowanie oraz kontrolę jakości. Oto niektóre z nich:
- DFMEA (Design Failure Mode and Effects Analysis) – analiza błędów w projektowaniu, mająca na celu identyfikację potencjalnych wad,
- PFMEA (Process Failure Mode and Effects Analysis) – analiza błędów w procesach, koncentrująca się na wykrywaniu i eliminacji usterek podczas produkcji,
- MSA (Measurement System Analysis) – analiza systemów pomiarowych, która zapewnia precyzję i powtarzalność pomiarów,
- SPC (Statistical Process Control) – statystyczne sterowanie procesem, umożliwiające monitorowanie i kontrolowanie zmienności za pomocą kart kontrolnych i diagramów Pareto,
- PPAP (Production Part Approval Process) – proces zatwierdzania części produkcyjnych, który gwarantuje zgodność z wymaganiami jeszcze przed rozpoczęciem produkcji seryjnej,
- QFD (Quality Function Deployment) – zarządzanie funkcją jakości, które przekłada potrzeby klienta na konkretne cechy produktu,
- Design of Experiments (DOE) – optymalizacja projektowania i produkcji poprzez eksperymentowanie oraz analizę danych, co pozwala na określenie kluczowych czynników wpływających na jakość.
Te narzędzia są nieodzowne w APQP, gdyż umożliwiają identyfikację potencjalnych problemów, monitorowanie zmienności, optymalizację parametrów i realizację działań korygujących. W efekcie prowadzą do ciągłego doskonalenia jakości produktów.
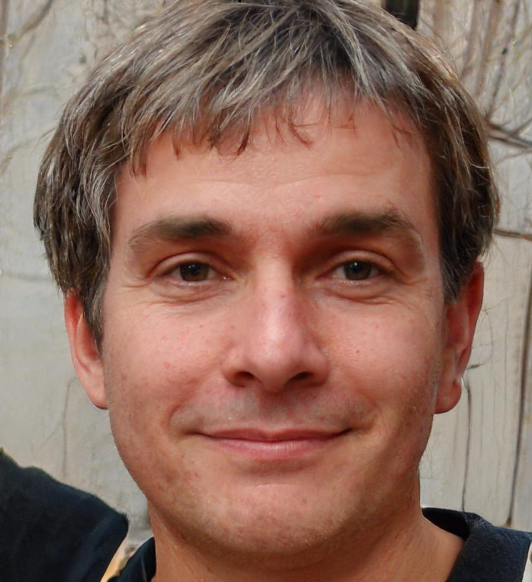
Nazywam się Jakub i jestem logistykiem z 15 letnim doświadczeniem. Pracowałem w różnych firmach i obecnie pracuje wyłącznie z domu obsługując zlecenia różnych firm. Na blogu dzielę się z Wami moją obszerną wiedzą o logistyce i produkcji.