PPAP, czyli Proces Zatwierdzania Części Produkcyjnych, odgrywa kluczową rolę w branży motoryzacyjnej, gwarantując jakość i zgodność produkowanych elementów. W artykule poruszono, dlaczego PPAP jest nieodzowny, jego cele oraz wymagania. Zawarto także opis etapów zatwierdzania i różne poziomy dowodów. Ponadto, omówiono wpływ cyfryzacji na PPAP oraz korzyści płynące z jego implementacji.
Co to jest PPAP i jakie ma znaczenie?
PPAP, czyli Proces Zatwierdzania Części do Produkcji, odgrywa kluczową rolę w przemyśle motoryzacyjnym jako istotny element zatwierdzania komponentów do produkcji masowej. Jego głównym zadaniem jest zapewnienie, że dostawcy są w stanie produkować części zgodne z wymaganiami klientów, co ma fundamentalne znaczenie dla zarządzania jakością oraz redukcji ryzyka produkcji wadliwych produktów.
Ten proces jest zgodny z międzynarodowymi normami jakości, takimi jak IATF 16949 oraz ISO, co podkreśla jego wagę w utrzymaniu wysokich standardów produkcyjnych. W sektorze motoryzacyjnym PPAP jest nieodzowny, aby zapewnić stabilność procesów produkcyjnych i tym samym utrzymać jakość na odpowiednim poziomie.
Dzięki PPAP producenci mogą mieć pewność, że ich wyroby spełniają oczekiwania klientów, co jest szczególnie istotne w kontekście globalnego łańcucha dostaw, gdzie priorytetem pozostają jakość i bezpieczeństwo.
Jakie są cele i wymagania PPAP?
PPAP ma na celu zapewnienie, że dostawca potrafi seryjnie wytwarzać części zgodne z wymaganiami klienta. Proces ten finalizuje się podpisaniem dokumentu PSW, co jest równoznaczne z akceptacją wymogów i gwarancją ich spełnienia. W sektorze motoryzacyjnym pełni on istotną rolę w minimalizowaniu ryzyka wadliwych produktów, zapewniając stabilność oraz wysoką jakość procesów produkcyjnych. Dzięki temu producenci mogą mieć pewność, że ich produkty odpowiadają oczekiwaniom klientów, co jest kluczowe w międzynarodowym łańcuchu dostaw.
PPAP wymaga spełnienia pięciu poziomów dowodów, które są uzależnione od specyfikacji klienta. Najczęściej wykorzystywany jest poziom trzeci, wymagający pełnej dokumentacji potwierdzającej zgodność z wymaganiami. Dokumenty te obejmują między innymi:
- analizy DFMEA i PFMEA,
- plan kontroli,
- wyniki badań,
- PSW.
Te elementy są kluczowe do zatwierdzenia jakości części i ich zgodności z obowiązującymi normami.
Jakie elementy zawiera proces PPAP?
Proces PPAP składa się z osiemnastu kluczowych elementów, które zapewniają jakość i zgodność produkowanych części. Do najważniejszych należą:
- DFMEA (Analiza Potencjalnych Wad i Ich Skutków),
- PFMEA (Analiza Potencjalnych Wad Procesu),
- MSA (Analiza Systemu Pomiarowego),
- SPC (Statystyczna Kontrola Procesu).
Każdy z tych elementów umożliwia wykrywanie i kontrolowanie ewentualnych problemów jakościowych.
Dokumentacja techniczna i plan kontroli również odgrywają ważną rolę w PPAP, pozwalając precyzyjnie określić wymagania oraz metody ich monitorowania. Raporty z kwalifikowanego laboratorium potwierdzają, że materiały oraz procesy spełniają obowiązujące normy. Próbki produktów i części weryfikują zgodność z oczekiwaniami klienta.
Wszystkie te elementy razem tworzą system, który utrzymuje wysokie standardy produkcji i minimalizuje ryzyko występowania wadliwych produktów.
Jak przebiega proces zatwierdzania w PPAP?
Proces zatwierdzania w ramach PPAP finalizuje się przez podpisanie dokumentu PSW (Part Submission Warrant), co stanowi istotny krok w procesie aprobaty części do produkcji masowej. Klient, na podstawie otrzymanej od dostawcy dokumentacji PPAP, podejmuje decyzję o akceptacji produktu. Ważne jest, aby dokumentacja była pełna i spełniała wymagania klienta, co gwarantuje, że części odpowiadają określonym standardom jakościowym.
Dział technologiczny odgrywa tutaj istotną rolę, oceniając, czy dostarczone dowody aprobaty są wystarczające. Możliwe jest nadanie różnych statusów:
- pełne zatwierdzenie,
- warunkowe zatwierdzenie,
- odrzucenie dokumentacji.
Warunkowe zatwierdzenie wskazuje na konieczność wprowadzenia działań naprawczych, aby uzyskać pełne zatwierdzenie. Jeżeli dokumentacja zostanie odrzucona, dostawca musi wnieść poprawki i ponownie przedłożyć dokumenty. Ten proces jest niezbędny dla utrzymania wysokiej jakości i zapewnienia, że części spełniają oczekiwania klientów.
Jakie są poziomy dowodów PPAP?
W PPAP, czyli Procesie Zatwierdzania Części do Produkcji, poziomy dowodów odgrywają istotną rolę w zapewnieniu wysokiej jakości komponentów. Istnieje pięć różnych poziomów, które różnią się w zakresie wymagań dotyczących dokumentacji i próbek:
- na poziomie 1 wystarczy przesłać dokument PSW do klienta,
- poziom 2 jest nieco bardziej wymagający, ponieważ wymaga dostarczenia PSW wraz z próbką części oraz częściowej dokumentacji,
- najczęściej stosowany jest poziom 3, który obejmuje PSW, próbkę części i pełną dokumentację, co pozwala potwierdzić zgodność z oczekiwaniami klienta,
- w przypadku poziomu 4 do PSW dołącza się dodatkową dokumentację, którą określa klient,
- ostatni, poziom 5, wymaga zarówno PSW, próbki produktu, jak i pełnej dokumentacji, która musi być dostępna u dostawcy.
Wybór odpowiedniego poziomu zależy od istotności danego elementu oraz jakości dostawcy, co ma na celu zminimalizowanie ryzyka uzyskania niezgodnego produktu.
Jakie są przyczyny przedłożenia PPAP?
Istnieje wiele przyczyn, dla których przeprowadza się PPAP, a wszystkie dotyczą istotnych elementów produkcji i zarządzania jakością.
- wprowadzanie nowych produktów na rynek,
- potwierdzenie, że dostawca potrafi wytwarzać części zgodne z wymaganiami klienta,
- zmiany technologiczne, jak nowe metody produkcji czy aktualizacje sprzętu.
Dzięki temu można mieć pewność, że nowa technologia nie wpłynie negatywnie na jakość wyrobów.
Gdy modyfikacje obejmują projekt lub materiały, warto przeprowadzić PPAP. To umożliwia ocenę, czy zmiany nie zaszkodzą funkcjonalności lub jakości końcowego produktu. Czasami to wymagania klienta dotyczące zatwierdzenia części stają się impulsem do przeprowadzenia PPAP, zwłaszcza gdy klient pragnie mieć pewność, że części spełniają wszelkie normy i standardy.
Zdarza się również, że sami dostawcy inicjują PPAP, aby zagwarantować jakość i sprostać wymaganiom klientów. Proces ten nie tylko zatwierdza nowe lub zmienione części, ale także służy jako narzędzie kontrolne, pomagając dostawcom utrzymać wysoką jakość produkcji.
Jakie korzyści przynosi PPAP?
PPAP oferuje wiele korzyści. Przede wszystkim zmniejsza ryzyko wystąpienia wad w produktach, co ma kluczowe znaczenie dla utrzymania stabilności procesów produkcyjnych. Klienci są usatysfakcjonowani, ponieważ części odpowiadają ich standardom jakości. Dodatkowo, ten proces pozwala na obniżenie kosztów związanych z reklamacjami, co jest ważne w kontekście zarządzania jakością.
Dzięki stabilnym procesom produkcji, potwierdzonym przez PPAP, dostawcy mogą dostarczać niezawodne komponenty. W rezultacie prowadzi to do trwałej współpracy i wzmacnia zaufanie klientów.
Jak cyfryzacja wpływa na proces PPAP?
Postępująca cyfryzacja znacząco wpływa na proces PPAP, wprowadzając elementy automatyzacji oraz model-based definition (MBD). Dzięki automatyzacji zarządzanie dokumentacją staje się prostsze, co przyspiesza wprowadzenie nowego produktu na rynek i ogranicza liczbę pomyłek. MBD umożliwia automatyczne generowanie raportów PPAP, redukując zależność od manualnych procedur. Przykładowo, liczba błędów w tych raportach zmniejsza się o 77%, co znacząco podnosi jakość i efektywność produkcji.
Cyfryzacja usprawnia również komunikację z klientami oraz monitorowanie zgodności z normami. Ułatwia współpracę różnych działów, co jest niezwykle istotne w branży motoryzacyjnej. Dzięki zaawansowanym narzędziom analizy danych możliwe jest szybkie wprowadzanie zmian i dostosowanie procesów produkcyjnych do nowych wymagań. W efekcie proces PPAP staje się bardziej elastyczny i dostosowany do współczesnych realiów rynkowych.
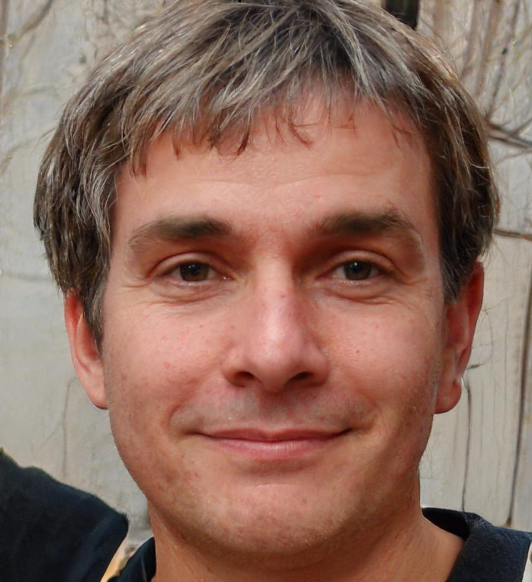
Nazywam się Jakub i jestem logistykiem z 15 letnim doświadczeniem. Pracowałem w różnych firmach i obecnie pracuje wyłącznie z domu obsługując zlecenia różnych firm. Na blogu dzielę się z Wami moją obszerną wiedzą o logistyce i produkcji.